Featured articles
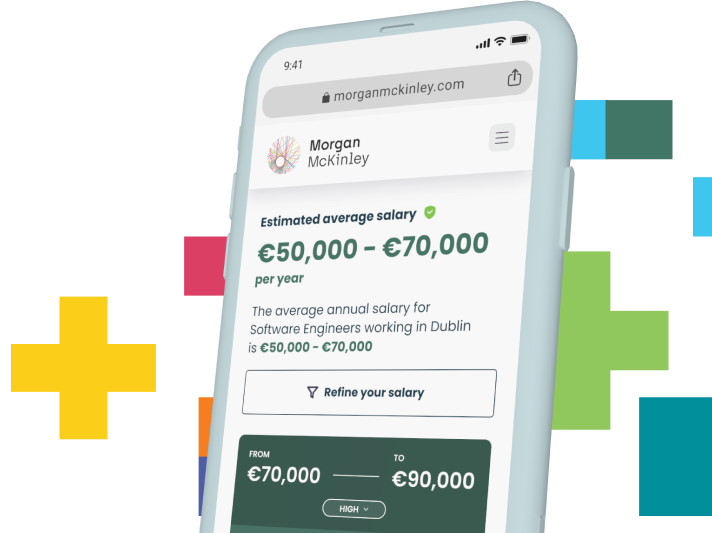
Latest articles
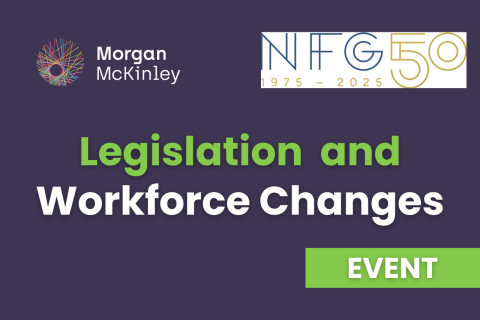
Legislation and Workforce Changes
Morgan McKinley, in partnership with NFG, are delighted to invite you to a morning with NFG Partner, Valerie Farrell and Associate Solictor Jillian O’…
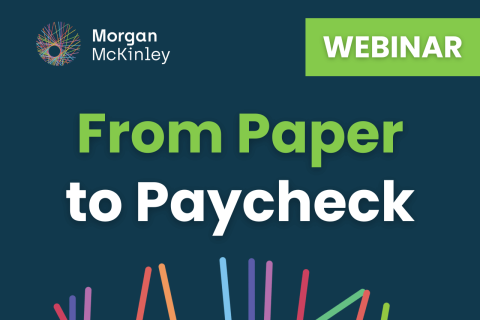
From Paper to Paycheck Webinar
Join Morgan McKinley Life Science experts in both contract and permanent roles for a lunchtime webinar to discuss the changing landscape of the current…
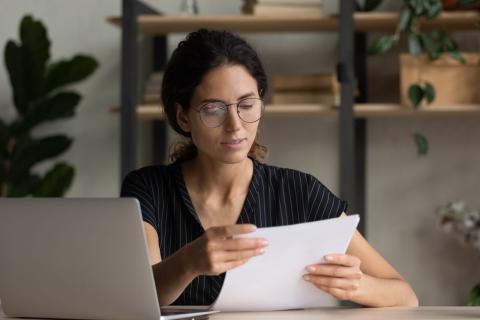
Key Contract Terms Explained: What to Know Before You…
Are you new to contracting? Does it feel overwhelming trying to understand all the terms in your contract?You’re not alone; many first-time contractors…
Considering a career move?
If you want to progress or even move into a new industry, browse our current vacancies to find your ideal job today.
VIEW ALL JOBS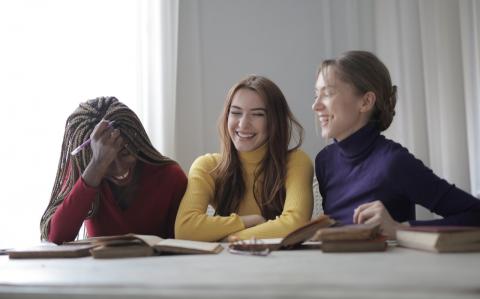
Becoming a contractor: The right move for your career?
More and more professionals are considering the temporary market when looking for work, seeking contracting jobs.
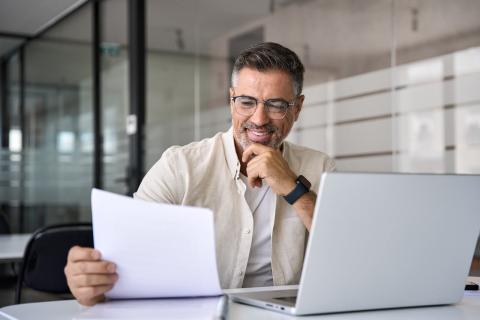
From Temporary to Trusted: Creating a High-Performing…
Your organisation is undergoing a digital transformation and you’re migrating from an outdated legacy system to a streamlined, fully automated process…
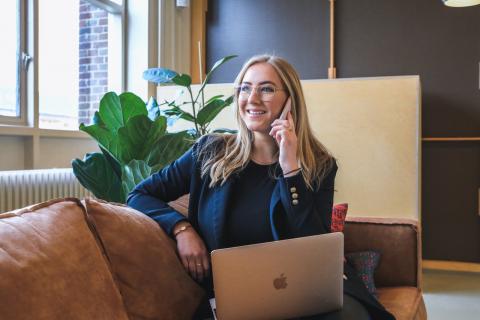
How To Attract And Recruit Contractors: 8 Things To…
Contract and temporary workforces are no longer just a contingency plan; they’re a strategic pillar in today’s workforce models.
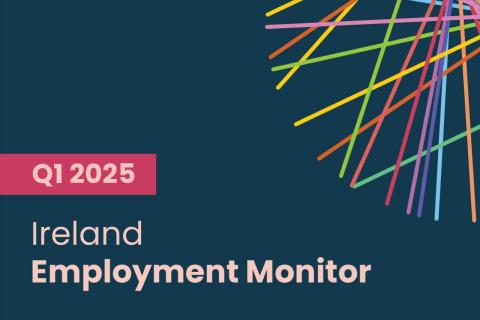
Morgan McKinley Ireland Quarterly Employment Monitor…
‘Quiet redundancies’ signal a subtle shift in workforce strategy AI reshaping how employers hire and evaluate talent
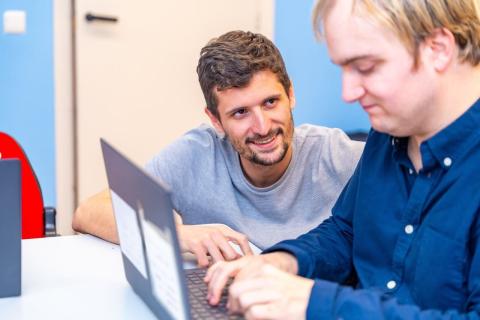
Inclusive by Design: An Employer’s Guide to…
In the years following Donald Trump’s rise to power in the United States, diversity, equity, and inclusion (DEI) policies around the world experienced…

Morgan McKinley Tokyo 20th Anniversary: A Celebration…
“You have entrusted us with your most precious resource- your people. You have allowed us to stand beside you through your journeys of growth,…
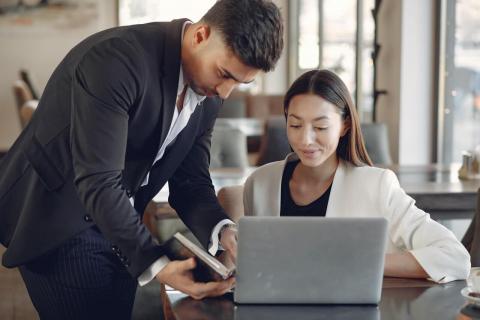
Which recruitment type is best for your hiring needs?
The time has come; you know your business needs to hire. Between your leaders, the department that needs new team members and HR, you’ve mapped out the…
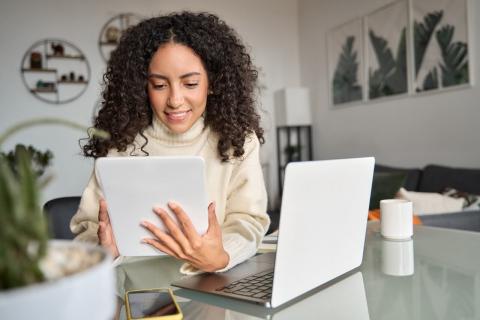
How to Use AI to Get More Interviews and Better Offers?
Job search can feel like a full-time job itself. Between searching for openings, customising your CV, writing cover letters, and preparing for…
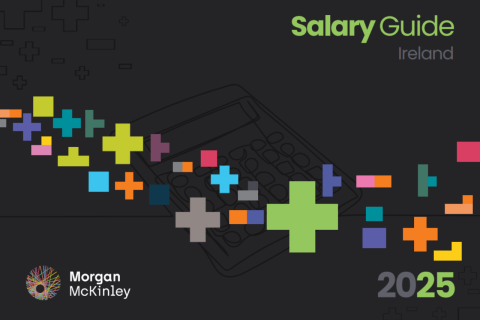
MODEST 2-3% SALARY GROWTH EXPECTED AMID ECONOMIC…
Days of across-the-board pay rises are over as firms prioritise critical skillsPay transparency progressing slowly as salary details in job ads remain…
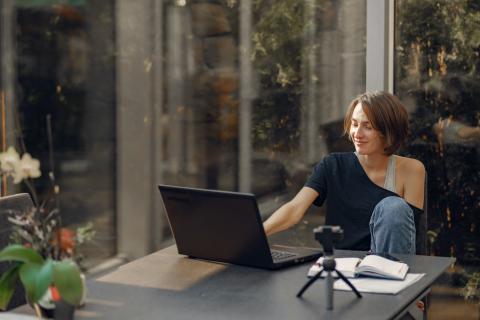
What the Data Says: Is Hybrid Work the Key to Employee…
Hybrid working; essential for a better work-life balance, or productivity inhibitor?
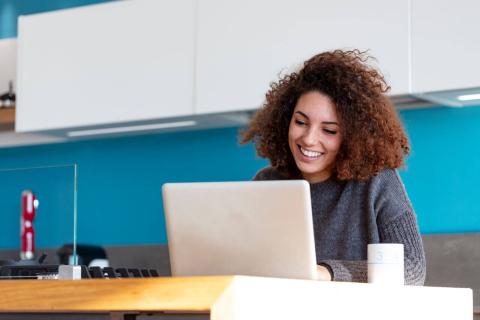
The Rise of the Four-Day Workweek: Productivity vs.…
This year, the UK has taken a significant step towards a four-day workweek. Two hundred companies have now permanently adopted this schedule without…
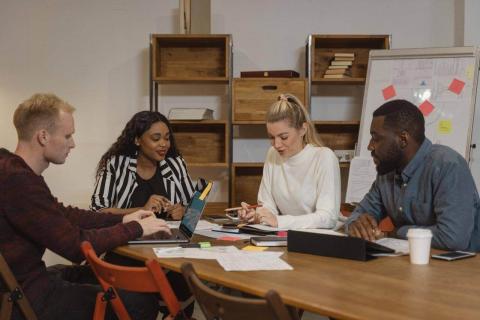
10 Of The Highest Paying Jobs In Ireland In 2025
Using data from our 2025 Salary Guide, we have outlined some of the highest-paying jobs in Ireland.
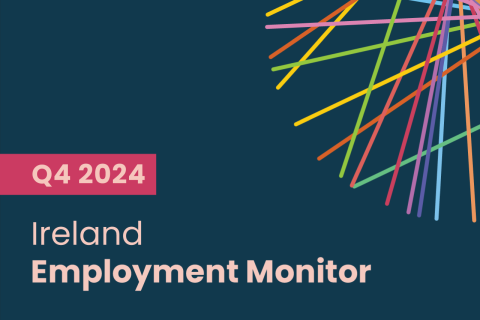
Morgan McKinley Ireland Quarterly Employment Monitor:…
Onsite work push, housing crisis, and rising costs slows job mobility Strong demand for niche skills, particularly in AI, automation, and…
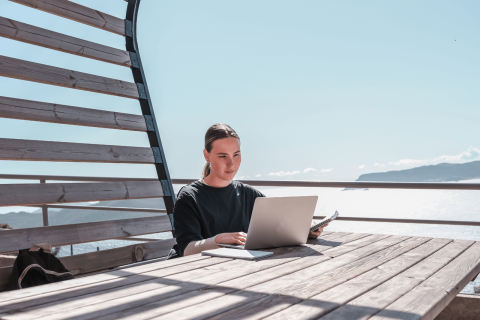
From Remote Work to Four-Day Weeks: The New Era of…
Recent pronouncements by prominent figures on work ethics and success have reignited discussions surrounding the significance of work-life balance.…